SunFMEA
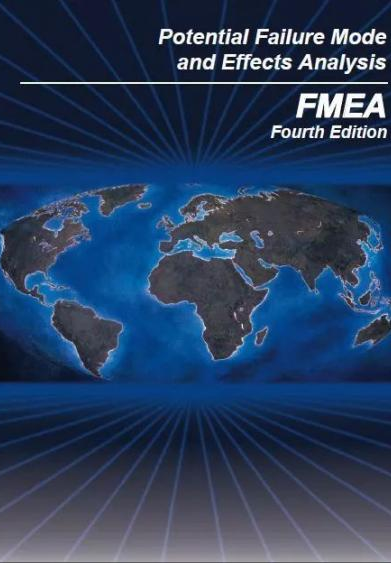
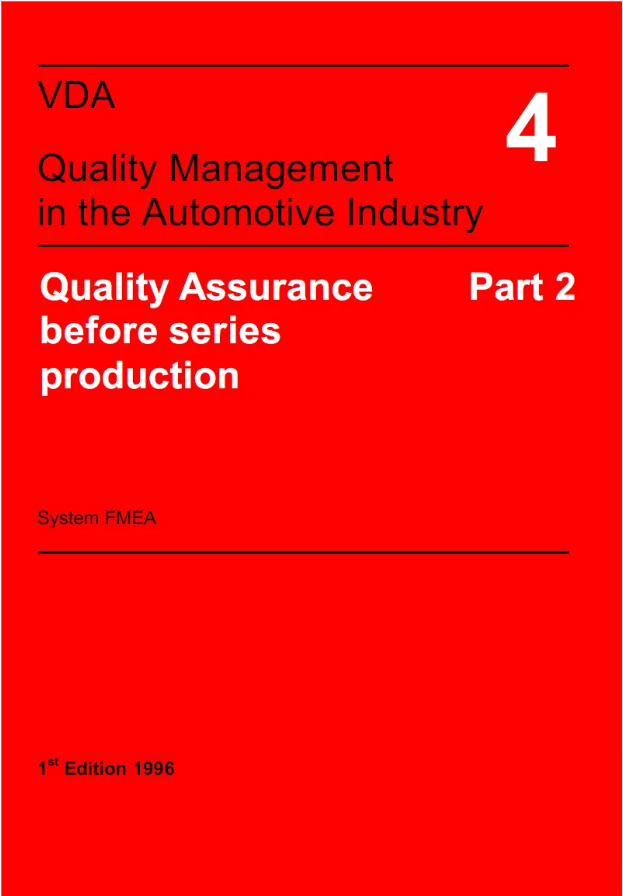
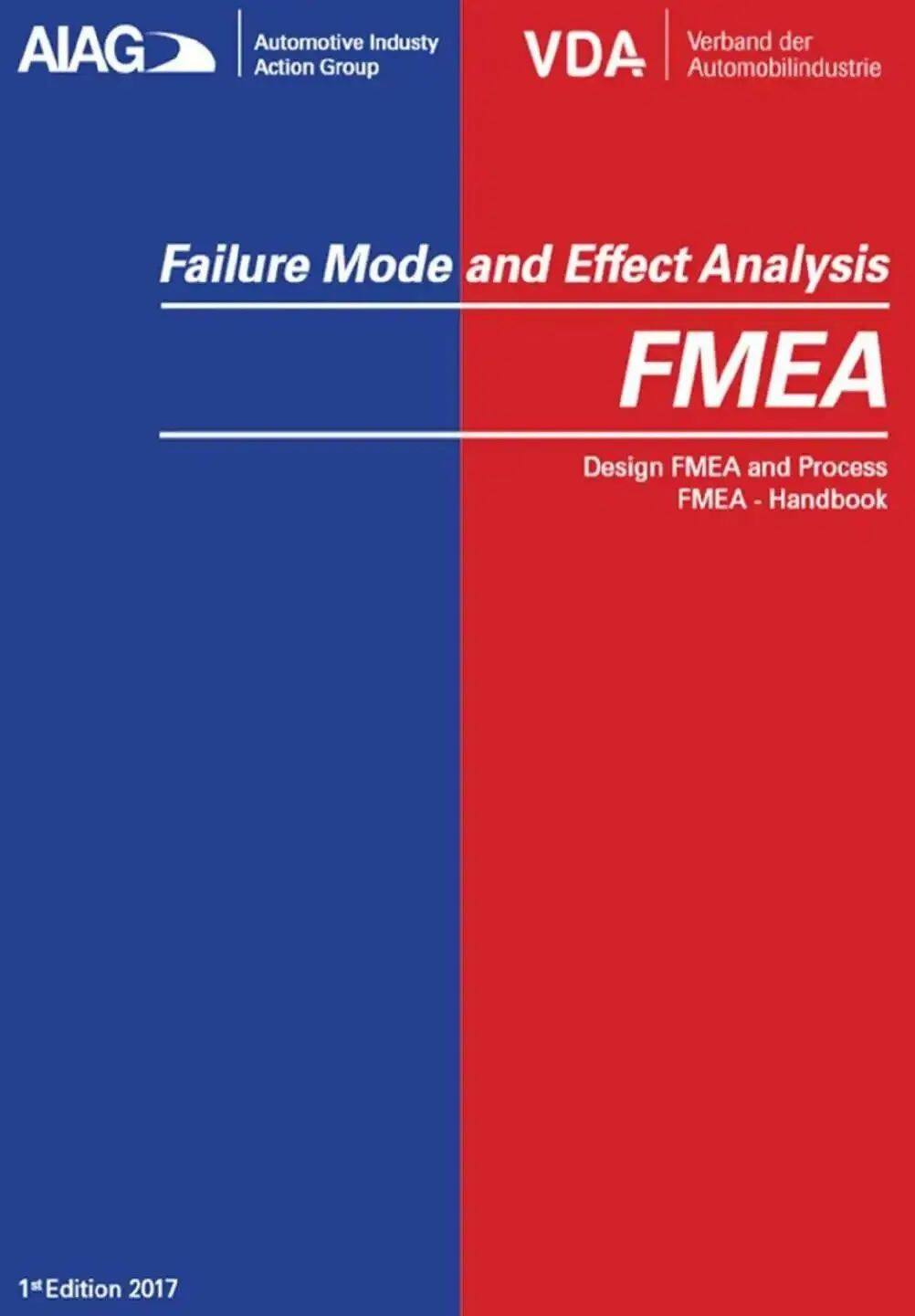
FMEA是一种可靠性设计的重要方法,是对各种可能的风险进行评价、分析,以便在现有技术的基础上消除这些风险或将这些风险减小到可接受的水平。它实际上是FMA(故障模式分析)和FEA(故障影响分析)的组合。
FMEA实际是一组系列化的活动,其过程包括:找出产品/过程中潜在的故障模式;根据相应的评价体系对找出的潜在故障模式进行风险量化评估;列出故障起因/机理,寻找预防或改进措施。
01 FMEA
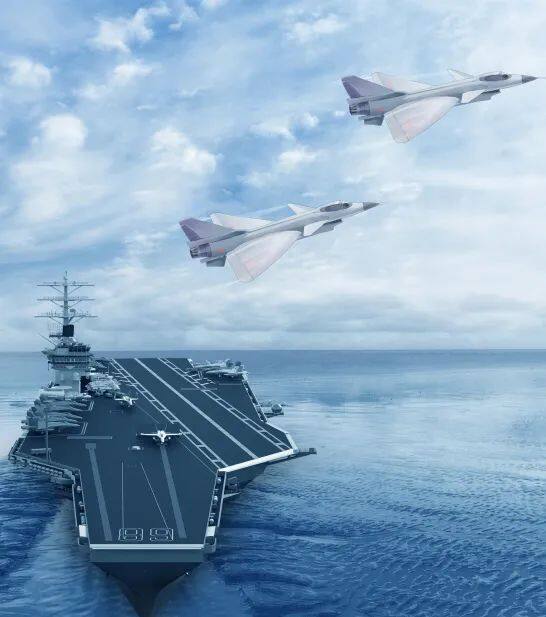
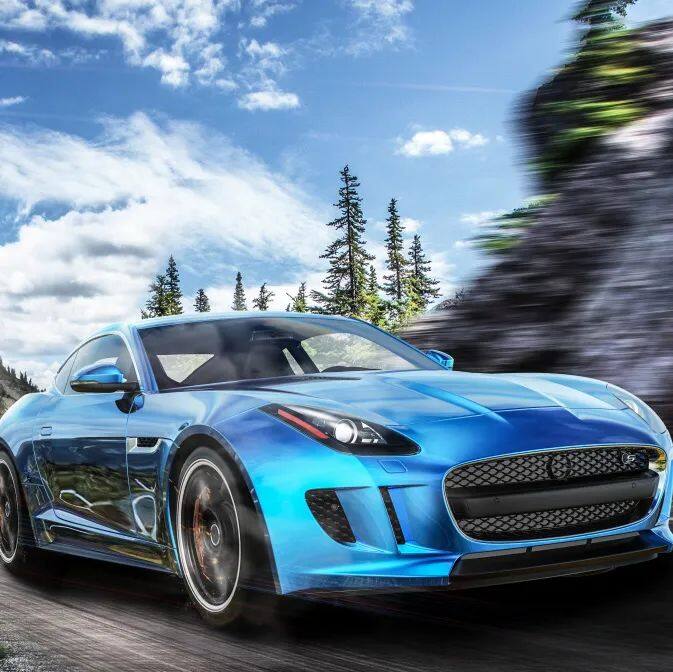
历史
History
50年代初,美国第一次将FMEA思想用于一种战斗机操作系统的设计分析;
60年代中期,FMEA技术正式用于航天工业(Apollo计划);
1976年,美国国防部颁布了FMEA的军用标准,但仅限于设计方面;
70年代末,FMEA技术开始进入汽车工业和医疗设备工业;
80年代初,进入微电子工业;
80年代中期,汽车工业开始应用过程FMEA确认其制造过程;
1988年,美国联邦航空局发布咨询通报要求所有航空系统的设计及分析都必须使用FMEA;
1991年,ISO-9000推荐使用FMEA提高产品和过程的设计;
1994年,FMEA成为QS-9000的认证要求。
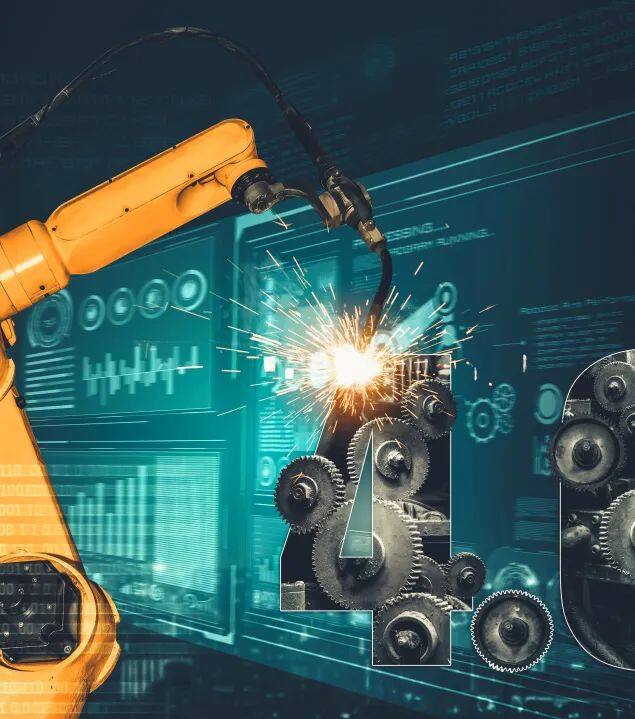
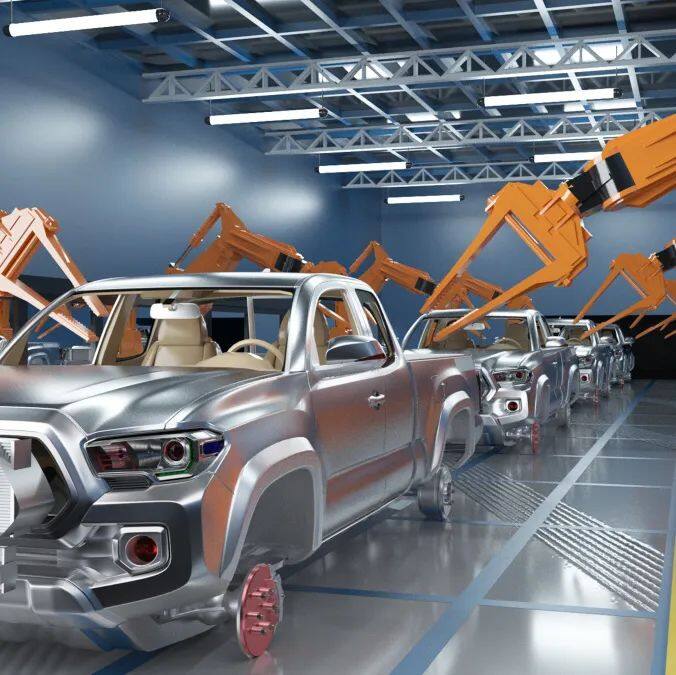
优势
Advantage
目的:
·能够容易、低成本地对产品或过程进行修改,从而减轻事后危机的修改。
·找到能够避免或减少这些潜在失效发生的措施;
益处:
·指出设计上可靠性的弱点,提出对策;
·针对要求规格、环境条件等,利用实验设计或模拟分析,对不适当的设计,实时加以改善,节省无谓的损失;
·有效地实施FMEA,可缩短开发时间及开发费用;
·FMEA发展之初期,以设计技术为考虑,但后来的发展,除设计时间使用外,制造工程及检查工程亦可适用;
·改进产品的质量、可靠性与安全性。
02 质量是设计出来的
不是测试出来的
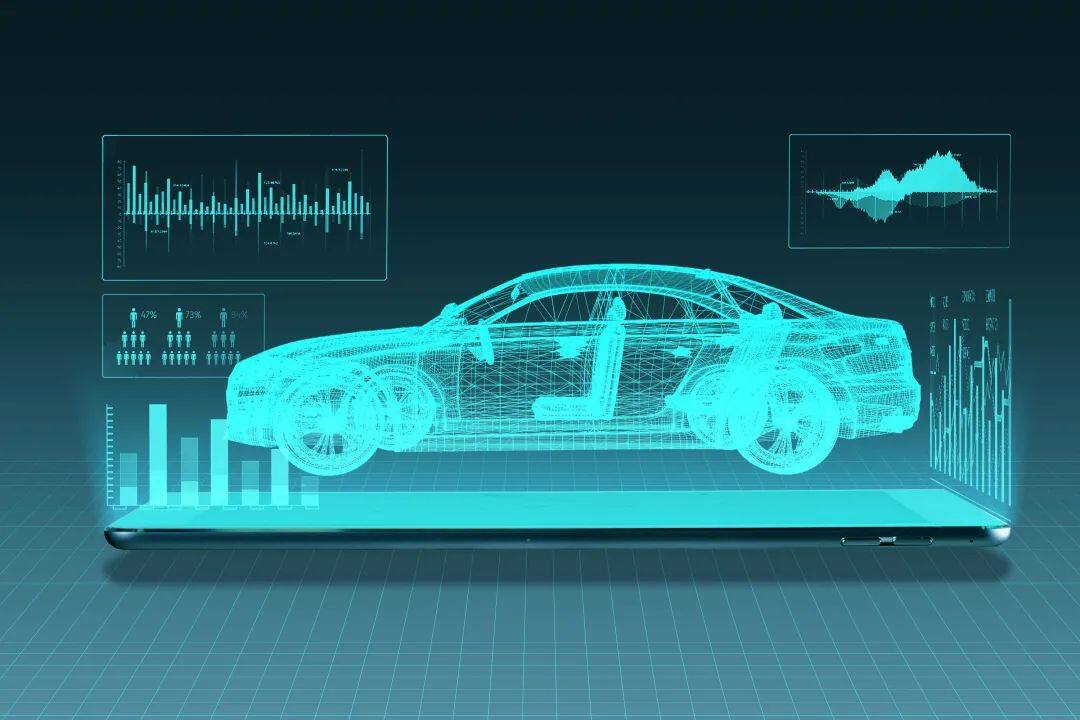
FMEA不单纯是一种故障后果防范的工具,更是一种设计理念。也就是说:在你设计电路或者设计软件的时候,就需要考虑某个部件如果损坏了,可能对系统的影响,并且在设计的时候就能够预见,并制定对策。
可靠性不是靠测试出来问题,解决问题实现的。而是设计出来的,也就是我们经常说的“质量是设计出来的”。在设计的概念阶段、就介入可靠性的设计,而在计划阶段和开发阶段的起始,就需要完成FMEA的分析报告。
1、帮助决策者从各种方案中选择满足可靠性要求的最佳方案;
2、通过系统级FMEA分析并确定系统最合理的可靠性架构,功能模块划分,冗余策略,复位策略,集中式/分散式控制策略等;
3、通过板级/器件级FMEA保证所有单元的各种故障模式及其影响都被周密考虑;
4、找出系统的可靠性薄弱环节,分析每个单元故障后对系统功能影响及其影响程度,为进一步改进产品可靠性设计以及可靠性定量计算提供资料。
产品的可靠性可以理解为三个规定,即规定条件下、规定时间内、产品完成规定功能的能力。
从用户的角度考虑,可简单地理解为几个层面的要求:
1、硬件不出故障;
2、硬件故障,仅对性能有部分影响,设备的功能不受损。
3、硬件故障,设备部分或全部功能受损。但能尽快恢复业务。
03 FMEA的基本思想
遍历性、系统性
我们可以在很多FMEA的教材上面看到这两个概念:遍历性、系统性。那么这两点在硬件设计的过程中是如何体现的呢?
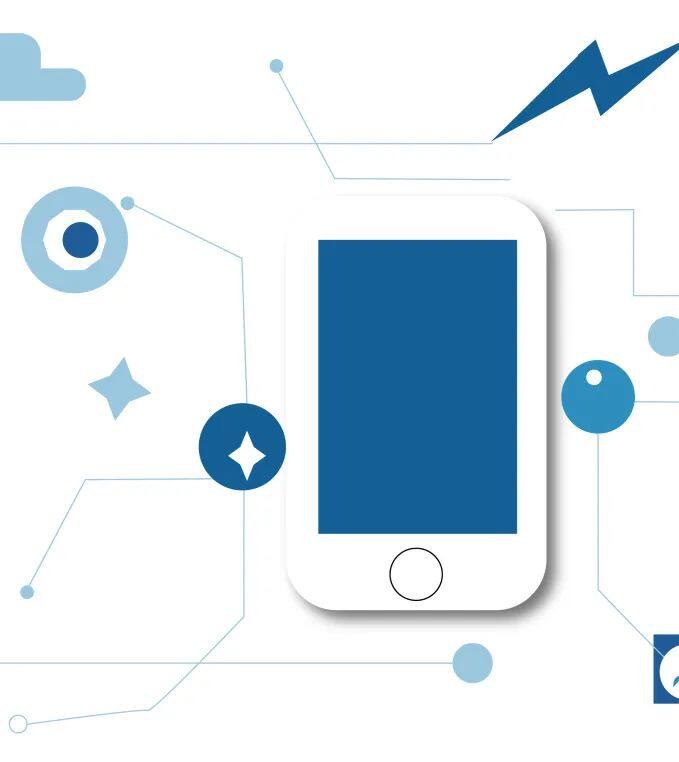
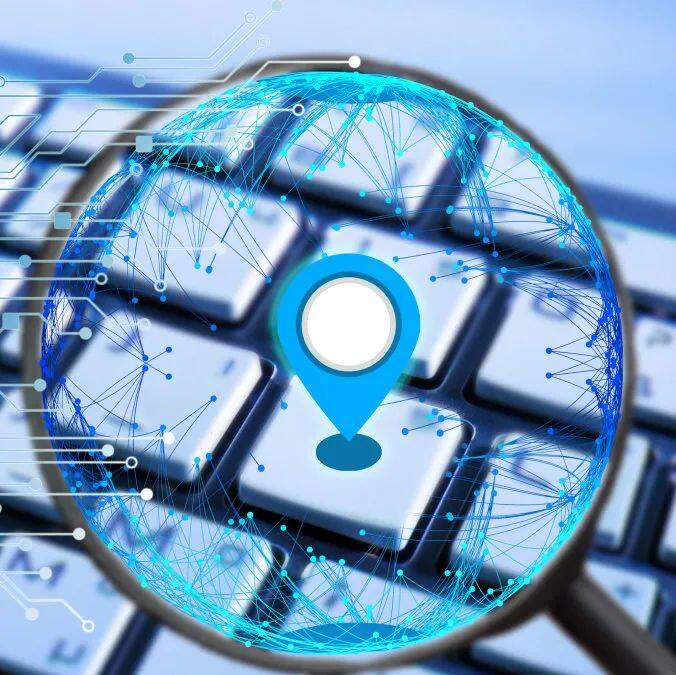
FMEA分析方法
Analysis
硬件法,从硬件的角度,对每个器件管脚输出分别去考虑故障模式、故障影响、检测补偿措施。(因为我们遍历了每一个器件、每一个器件的每一个管脚,所以这里体现了遍历性)
功能法,每个产品可以完成若干功能,而功能可以按输出分类。这种方法将输出一一列出,并对它们的故障模式进行分析,对应系统级、单板级分析。(此处按照功能和场景,对故障模式分别进行遍历和分析)。
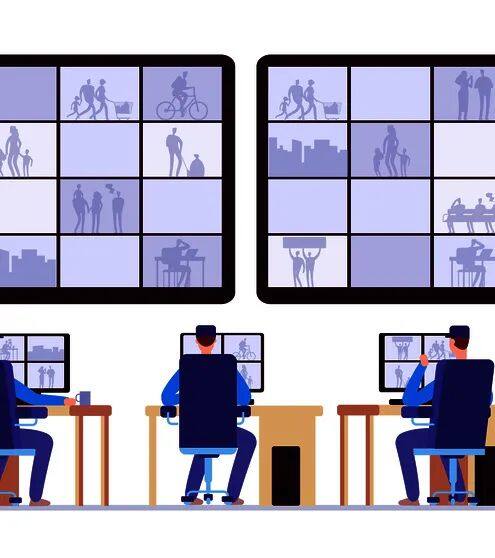
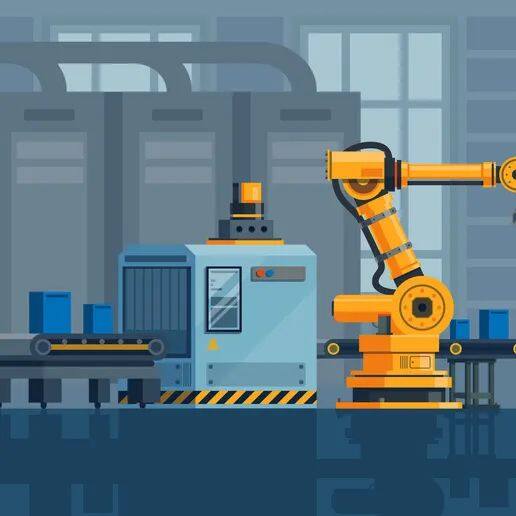
操作步骤
Operating Steps
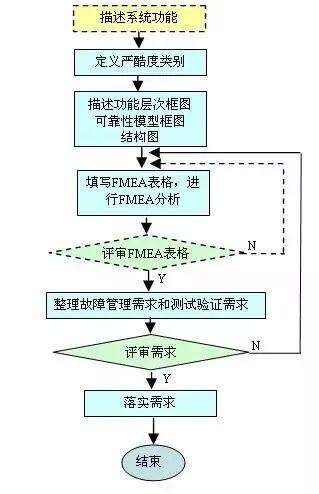
严重等级:
1、这种故障会导致整个系统崩溃或主要功能受到严重影响;
2、这种故障会导致系统主要功能受到影响、任务延误的系统轻度损坏或存在较大的故障隐患;
3、系统次要功能丧失或下降,须立即修理,但不影响系统主要功能实现的故障;
4、部分次要功能下降,只需一般维护的,不对功能实现造成影响(一般告警或指示灯故障等)。
描述结构图 :
清晰功能模块之间的相互关系,主要输入/输出信号。
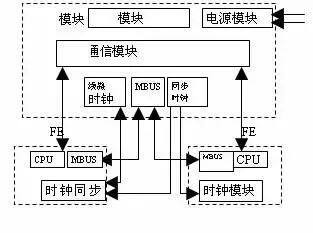
参考的FMEA表格:
开发过程中,如果急于出成果,那么做成的硬件精品,往往忽略一些功能设计之外的考虑,最后就可能导致返工。所以说可靠性设计,包含FMEA的设计是很重要的。磨刀不负砍柴工,从设计阶段,就融入可靠性、预防失效的思考,让你的设计上升一个台阶。
我们公司的质量是要靠检验的,制造只管造
[s-68]